製造業向け生産管理システム 受託開発 導入事例 株式会社近藤鐵工所 様
製造の進捗管理・可視化、より正確な原価管理を実現。
業務効率化や製造原価の低減に繋がりました。
- 導入製品
- 製造業向け生産管理システム 受託開発
- 業界/業種
- 工作機械のATC装置(自動工具交換装置)の部品製造
- 従業員数
- 58名(2025年3月現在)
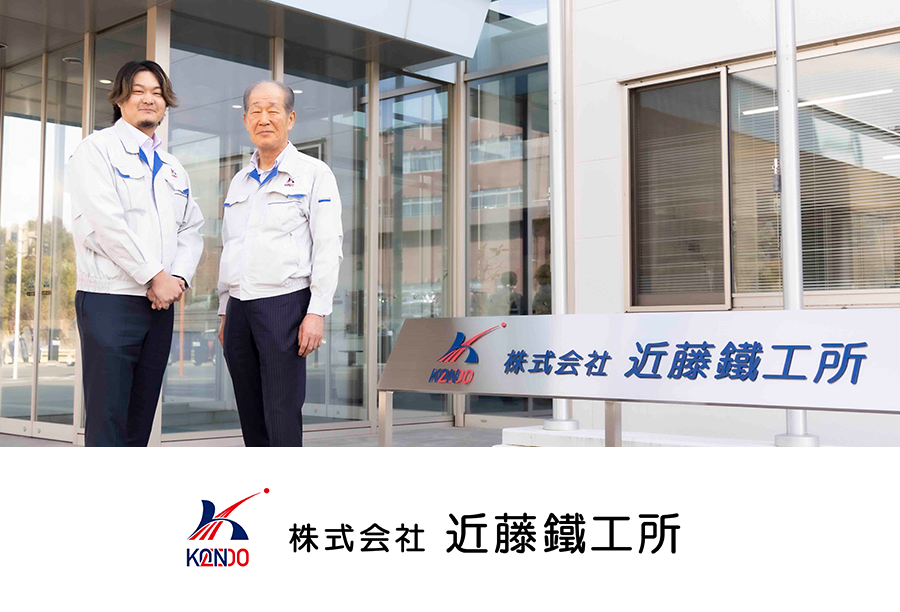
-
- 変種変量生産へと生産形態が変わっていく時代の中で、変化に合わせたシステムを構築。更なる利益向上へ。
- ハンディターミナルを活用し、より正確な労務費の算出ができる仕組みを導入。細かな原価管理でコスト見直し、削減へ。
- 進捗管理業務を手作業から自動化へ。リアルタイムに状況を把握し、進捗確認作業の負荷を軽減。
導入の背景・目的
ロット生産から変種変量生産へ。事業内容の変化に合わせた生産管理システムを構築。
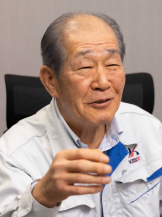
-- はじめに貴社の事業内容について、お聞かせください。
近藤昌泰氏:当社は1946年に近藤鉄工所として創業しました。1979年からは大手工作機械メーカー様との取引を開始し、工作機械に装着して使われるATC(Automatic Tool Changer)装置を中心に生産を行っています。
ATC装置は、いわゆる自動工具交換装置で、工作機械が加工作業する際の工具を、対象物の形状や素材に合わせて自動で交換する機械です。取引先のメーカーから週次で生産計画を受け取り、それに基づいて2か月先の納品をターゲットに所要量計画を立案・調整し、部品の調達・加工、組み立てというプロセスを経て納品しています。
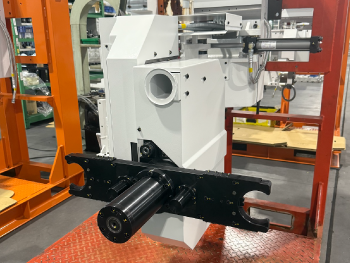
ATC装置
-- 貴社が生産管理システムの構築を決められたきっかけを教えてください。
近藤昌泰氏:候補企業もともと、1990年頃に、部品の工程管理が出来る仕組みをニッセイコムに構築してもらい、導入しました。その仕組みが大きく変わったのが2002年頃です。取引をしている大手工作機械メーカーがロット生産から変種変量生産に生産形態を変えたことで、当社も従来のロット生産から変種変量生産に対応できるように新たにMRP(資材所要量計画)の導入を検討し始めました。当時、ニッセイコムには変種変量生産についての知見を持つSEが在籍しており、システム構築の実績もありました。そこで、当社のニーズに基づいた最適な設計を一緒に検討してもらい、システムの導入に至りました。
それから現在に至るまで、環境の変化など、節目ごとにニッセイコムと議論を重ね、原価管理や進捗管理など段階的にシステムを改良してきました。
生産管理システムの機能とメリット①
ハンディターミナルとバーコードを用いた"より正確な労務費の算出"
-- 生産管理システムの特徴的な機能と活用メリットについて、お聞かせください。
近藤昌泰氏:より正確な製造原価を把握するために、原材料費だけでなく、細かな労務費も含めた原価管理を実現していることです。それが当社の利益の確保、原価低減のために必要だと考えたからです。
例えばメーカー様から当社に発注いただくATC装置には各々受注単価があり、単価が大きく変わることはありません。そのため"1台1台の製造コストをきちんと把握し、どうコストを抑えながら作るのか"が利益を上げる上で重要なポイントです。正確な原価管理を行うことで、コストのかかる工程と改善効果の大きい部分を把握し改善することができ、原価低減、利益確保に繋げられます。
この正確な原価を算出するための工夫の一つとして、"より正確な労務費を算出すること"が挙げられます。
-- 具体的にどのように労務費を算出されているのでしょうか。
近藤昌泰氏:ハンディターミナルと作業伝票のバーコードを活用しています。当社は作業伝票を使って、工場の作業担当者に作業内容を指示しています。例えば部品加工の工程なら、作業伝票には、作業担当者、加工する部品名、数量などが記載されています。
2019年、この作業伝票に記載されている情報と紐付くバーコードを追記し、ハンディターミナルを導入しました。部品加工の現場では、作業担当者が、7~8つある各工程の作業開始時と終了時に、ハンディターミナルでバーコードをスキャンします。これによって人単位での作業時間を正しく計測することができ、より正確な労務費を算出することが可能となります。
原材料費や物流コストに加えて、正確な労務費を算出できるようにしたことで、より正確な製造原価も把握できるようになりました。これは今後、各原価項目をさらに削減していく取り組みに繋げていくことができると考えています。
生産管理システムの機能とメリット②
リアルタイムな進捗管理で工程確認作業の負担軽減
-- 製造工程の進捗管理業務も効率化されたとお伺いしました。その詳細について、お聞かせください。
近藤昌泰氏:製造工程の見える化の大きな特徴は、進捗状況が自動で情報反映され、リアルタイムに進捗状況を把握できる点です。加工工程・組立工程の両方で見える化を実現しました。
加工工程では、作業管理者が部品加工プロセスの進捗状況を、パソコンや作業現場に設置した大型ディスプレイを使い、一目で把握できる仕組みを構築しました。ハンディターミナルと作業伝票に追記したバーコードで、作業の開始時間と終了時間が把握できるようになったので、そのデータを使って進捗状況を見える化しました。
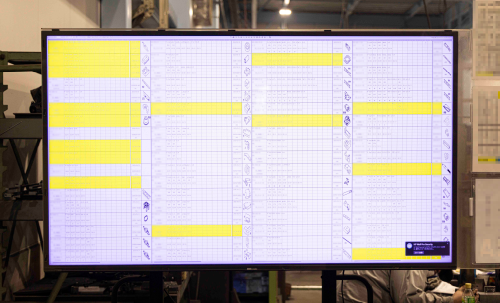
加工工程の作業場に設置してある大型ディスプレイ
加工工程の進捗状況が確認出来る
従来の進捗管理では、作業管理者が何枚ものA3用紙に部品ごとの製造工程を並べてプリントアウトし、週単位で修正して出力し直すという作業を繰り返していました。紙ベースの運用なので手間も時間もかかっていました。また、以前は作業管理者が現場を回り、作業担当者一人一人に声を掛けて遅れていないかどうかを確認し、遅れているようならさらに前の工程の現場に足を運んで、遅れている理由を聞いていました。
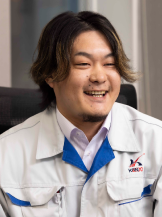
作業管理者がオフィスのパソコンなどで進捗状況を把握できるようになったことで、紙で出力する運用と比べて、2時間の作業が不要になりました。また、遅延している工程も簡単に特定できるようになりました。進捗管理業務の大幅な効率化に繋がっています。
近藤寛幸氏:組立工程でも進捗状況が一目で把握できるようにしています。加工部門と同様にハンディターミナルと作業伝票のバーコードを活用して進捗管理の見える化を実現しました。組立工程では作業が並行して進むので進捗状況の見える化が難しいのですが、作業が完了している工程には自動で色が付くなど、一目で今の状況が分かるようになっています。
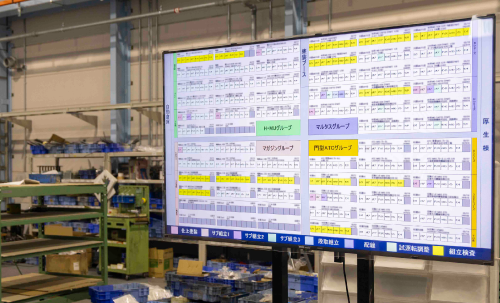
組立工程の作業場に設置してある大型ディスプレイ
組立工程の進捗状況が確認出来る
-- ちなみに貴社では、進捗状況確認リストを作成し、加工する部品のポンチ絵を記載されていると伺いました。その理由は何でしょうか?
近藤昌泰氏:現場の作業担当者にどんな部品を加工するのかを、まず直感的に伝えるためです。
進捗状況確認リストは、作業担当者が未完成部品の作業進度を確認し、作業を進めるためのものです。部品番号だけではどんなものを作ればいいのかイメージがつかめません。そこで、進捗状況確認リストにポンチ絵を載せることで、直感的に作業担当者がどんな部品を加工すればよいか、イメージできるようにしています。
この取り組みは生産管理システム導入前から行っていましたが、システム導入のタイミングで電子化し、ポンチ絵も載った進捗状況確認リストが発行されるようになっています。
生産管理は一般の人からすると分かりにくい言葉や内容が多いのですが、「誰が見ても分かりやすい仕組みにしたい」という私の想いをもとに、システムを構築してきました。ポンチ絵もその1つです。誰が見ても分かりやすいようにしています。
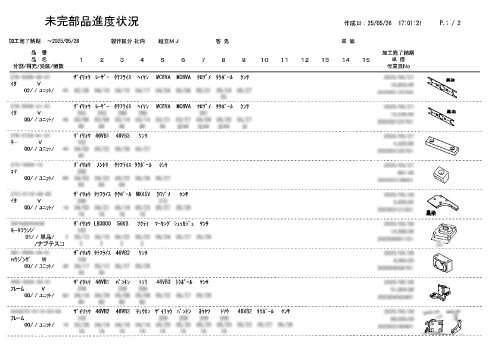
進捗状況確認リスト
今後の展望
ニッセイコムの支援を受けてAIなども活用し、機械割り当て作業の自動化を実現したい
-- 貴社は2021年8月に新工場を新設されました。今後の展望と、その中でニッセイコムに期待されることなどについて、お聞かせください。
近藤昌泰氏:私には、「システムでできることはシステムがやって、人間にはものづくりに専念して欲しい」という想いがあります。ニッセイコムからのアドバイスもあり、一気にシステム化するのではなく、小範囲でシステム化をして現場が慣れたらまた次のシステム化と、少しずつステップアップしながらやってきました。
そのような中、次に取り組みたいと考えているのが、機械割り当て作業の自動化です。
これは私の大きな課題の1つで、将来的に「部品加工における負荷の平準化」を実現したいと考えています。
納期を守るためには、「機械A」にばかり負荷がかからないように「機械B」や「機械C」を用いる、あるいは「外注に依頼する」など、部品を取りそろえるまでの調整が非常に重要です。ここを平準化することが一番スムーズに事業が流れることに繋がっています。現状は機械割り当て等の負荷調整は人が手作業で行っていますが、今後はこの作業をシステムで自動化させたいと考えています。
今後5年後、10年後には、AIが企業で当たり前に使われるツールになると思います。当社もAIを活用して機械の割り当てを自動化し、作業負荷の平準化を実現したいと考えています。ニッセイコムには引き続き、心強い支援を期待しています。
お忙しい中、ありがとうございました。
お客様プロフィール
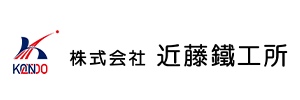
1946年の創業以来、「ものづくり」へのたゆまぬ探究心と創造力で、工作機械や自動車部品分野で取引業界を通じた社会貢献を続けている。2021年8月末には、新たなる飛躍に向けて工作機械の一部となるATC装置(自動工具交換装置)の製造工場を完成させ、"新生近藤鐵工所"づくりをスタートさせた。
- 事業内容
- 工作機械のATC装置(自動工具交換装置)の部品製造・加工ならびに装置組立、自動車部品の加工
- 所在地
- 愛知県蒲郡市水竹町下沖田10番地4
- 法人設立
- 1986年9月3日
- 従業員数
- 58名
- Webサイト
- 株式会社近藤鐵工所
- 取材日
- 2025年3月
本事例に記載の情報は取材日時点のものであり、本ページ閲覧時には変更されている可能性があることをご了承ください。